Abrasive blasters who have properly sized air compressors have the best chance for maximizing productivity and efficiency. Contractors and others who blast with mismatched air volume can suffer lost productivity and profits.
Read more >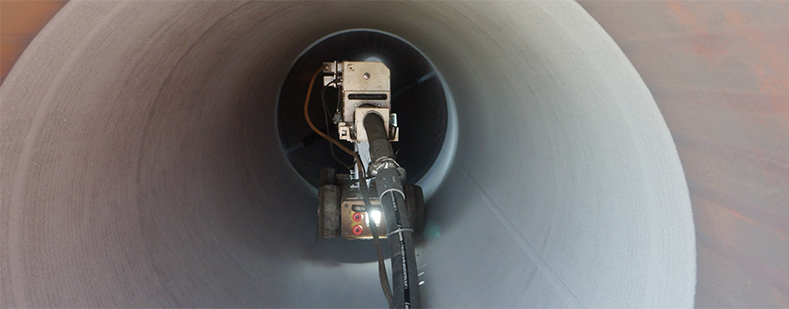
As contractors and facility managers look for ways to save money, reduce waste, and increase worker safety on abrasive blasting projects, robotic abrasive blasting is becoming more prevalent. Robotic blasting allows for precise control, high productivity rates and reduced abrasive media consumption compared to manual blasting. In addition, robotic abrasive blasting is a safer alternative to manual blasting.
Read more >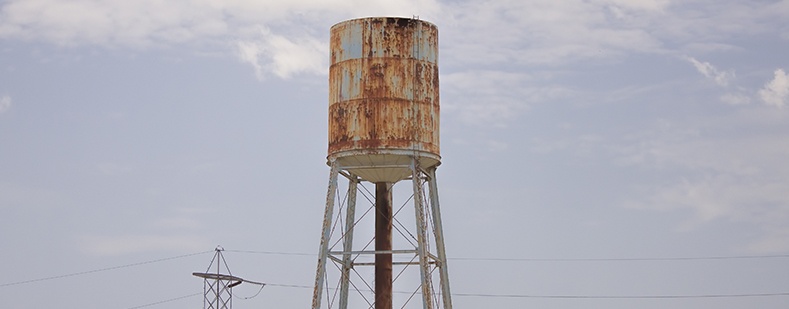
Imagine for a moment that ACME Coatings Contractor has recently completed an important water tank exterior coatings project. The job, which involved removing lead-based paint from the 40 meter (135-ft) tall, 3.7-million liter,legged tank, went well from start to finish. The owners are happy, final payment has been rendered, and the project manager is filing the last bit of paperwork when the owner’s representative calls and asks, “Out of curiosity, how can we be sure that ACME didn’t leave lead dust under or around the tank?”
Read more >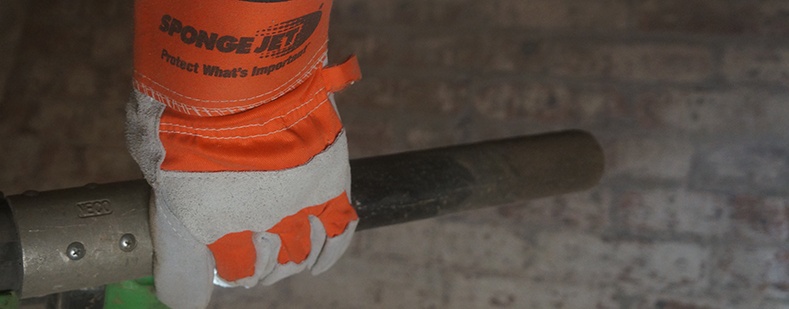
B. C. Tilghman: The Father of Sandblasting and Abrasive Nozzles
The process of sandblasting as we know it today started around 1870 with a man named Benjamin Chew Tilghman, who observed abrasive wear on wind-blown desert windows. Tilghman also noticed the effect that high-velocity sand could have on hard material and began designing a machine that could propel sand at speeds much faster than the wind - and could concentrate this flow into a small stream.
Read more >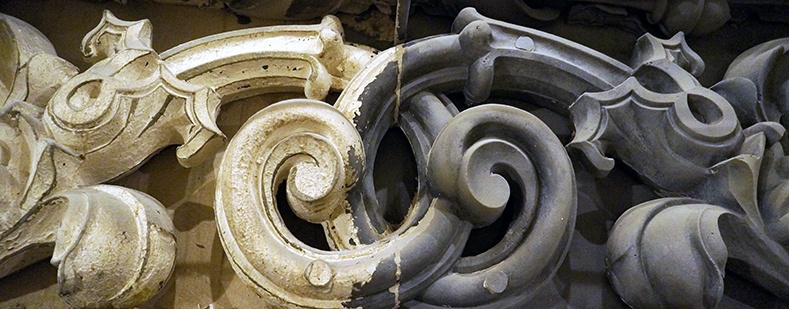
When making decisions regarding lead abatement, facility managers naturally consider a whole host of complex variables. Their recommendations will be used to ultimately decide whether lead-coated surfaces be enclosed and encapsulated, replaced—or removed altogether.
Read more >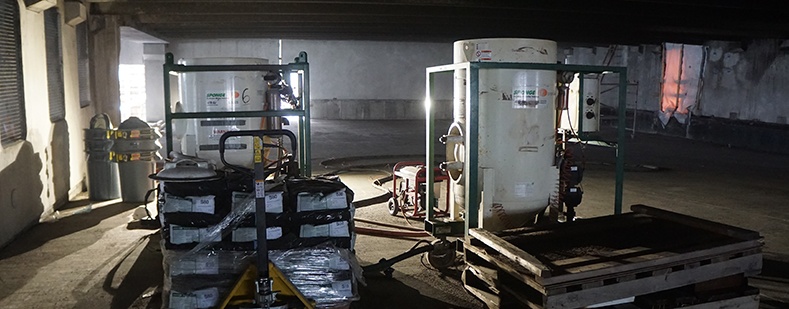
Sandblasting (or abrasive blasting as it’s more properly known) was invented in the late 19th century. The simple process of introducing abrasive into a stream of air and propelling it at high velocity onto a surface has grown with the advancement of technology. Equipment can be as basic or as specialized as desired.
Read more >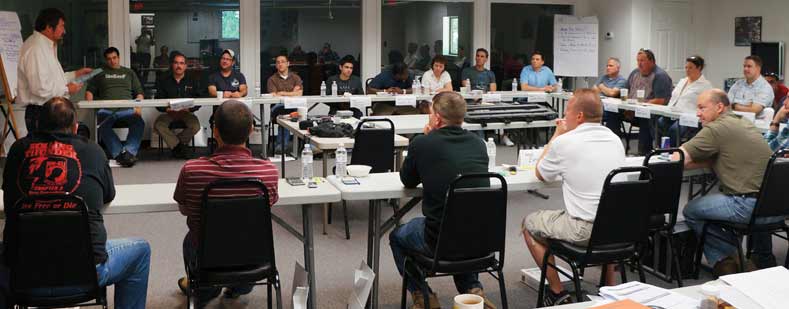
The Sponge-Jet Global Training and Technology center has published its 2018 Third-Party class schedule which features a broad range of accredited classes from leading industrial trade associations like the National Association of Corrosion Engineers (NACE International), The Society for Protective Coatings (SSPC) and committee meetings which include the American Society for Testing and Materials (ASTM).
Read more >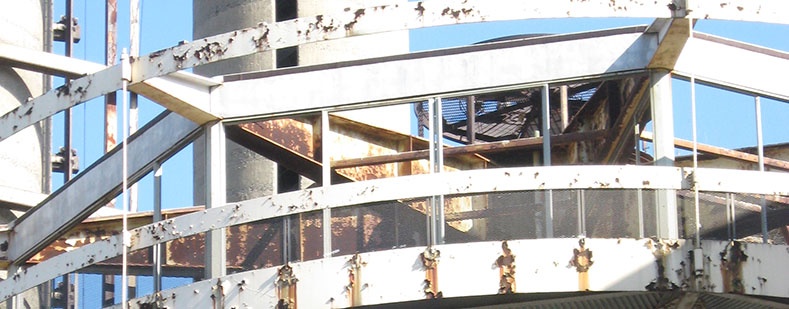
Surface Preparation (or Surface Prep for short) is the process of cleaning and readying surfaces for new coatings. Due to varying attributes and performance characteristics of the many coating types, surface preparation requirements can also be unique from project to project. As a result, it’s very important to always read the coating specification and all coating technical data sheets.
Read more >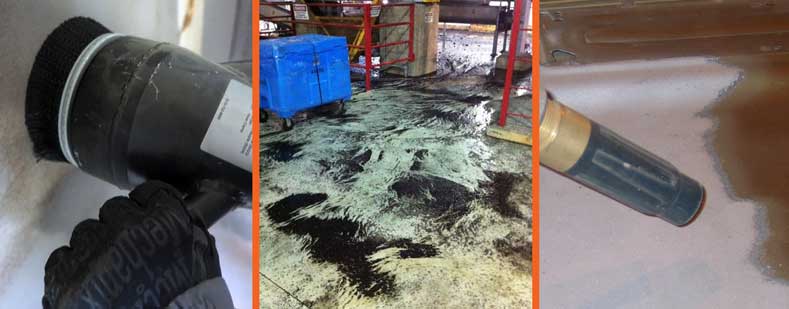
Dust is a notorious side effect of abrasive blasting. Blast nozzles introduce a tremendous amount of air to a small area, whipping small pieces of grit, many hundreds of miles per hour into a surface that may be very dirty. As abrasive media come into contact with a substrate, dust is created as the coating is removed, as the abrasive profiles the substrate, and as the abrasive shatters.
Read more >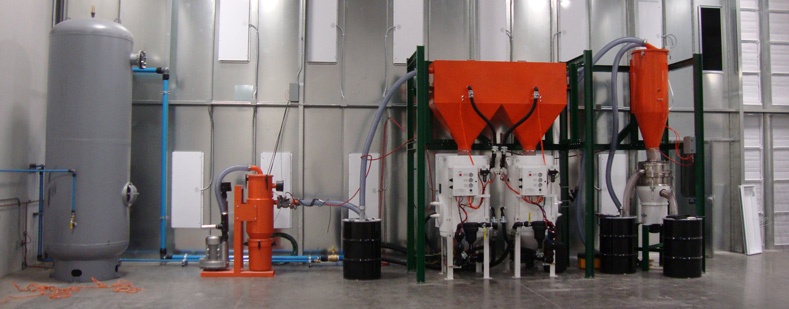
Sponge-Jet is phasing out modular sound-proof blast room and dust collectors which have previously been part of our KwietKave™ product line. Sponge-Jet will continue to offer all other stationary blasting, vacuuming, recycling and reloading solutions –now called Sponge-Jet Custom Integrations™replacing the KwietKave branding.
Read more >