Many manufacturers are turning to Sponge-Jet products for their surface preparation needs. With safety and efficiency as a top priority, these facilities are looking for ways to perform necessary surface preparation projects while avoiding shutdown and blasting near both sensitive equipment and other trades nearby.
Read more >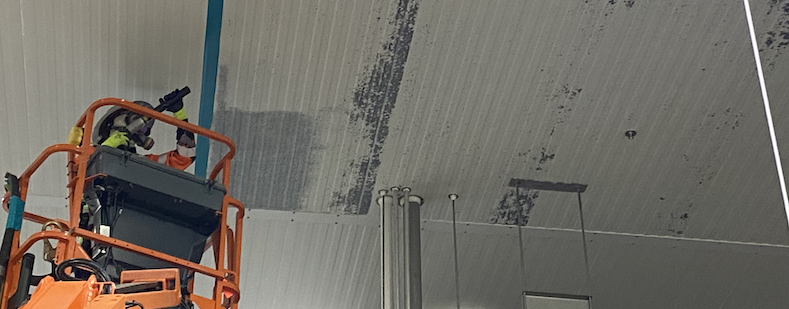
Whether painting delicate surfaces like tin ceilings, or industrial surfaces such as machinery or roof decking, the quality and longevity of the paint job relies on the surface preparation before coating. On large square footage painting projects, surface prep is often the least considered step, but in reality, it’s the most crucial and plays a key role in the overall success of the paint job. Investing time and effort in this stage is essential to achieve lasting, high-quality results.
Read more >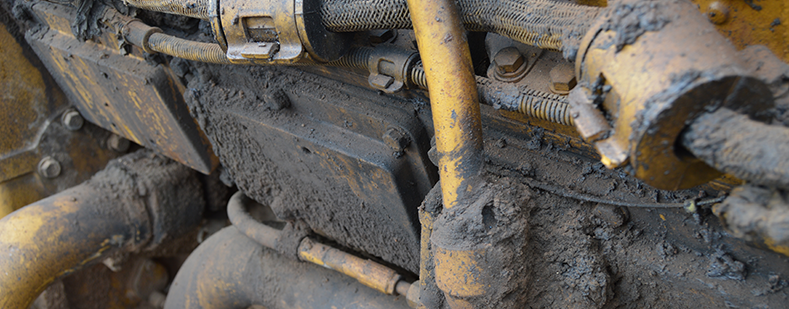
Early coatings failures can often be attributed to inadequate surface preparation. One of the most common steps skipped prior to applying a new coating is failing to effectively remove grease and oils from the substrate prior to painting.
Read more >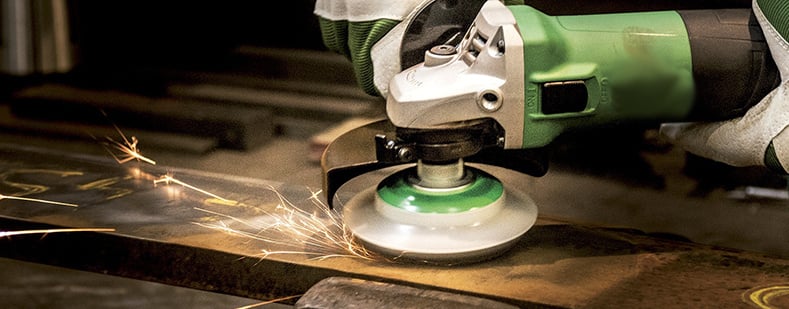
Power tooling is a method of surface preparation commonly used in tight spaces where access is limited. Pneumatic, electric, and hand tools such as angle grinders, needle guns, wire wheels, wire brushes, scrapers, and sanding pads can be used to remove rust, paint, and other contaminants from a surface.
Read more >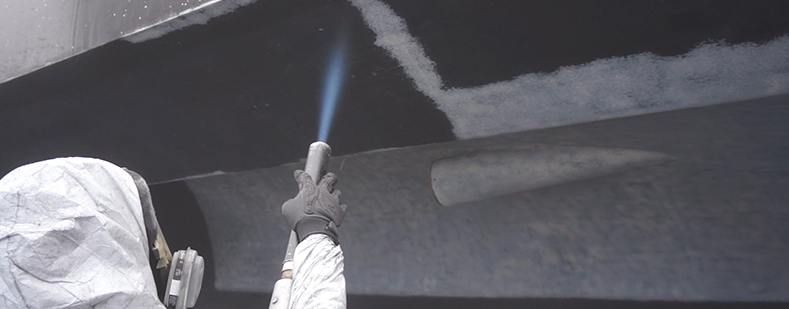
Painting a surface might seem like a straightforward task, but the key to a long-lasting and visually appealing finish lies in surface preparation. Whether you're dealing with metal or concrete, investing time and effort in preparing the surface before applying paint is essential.
Read more >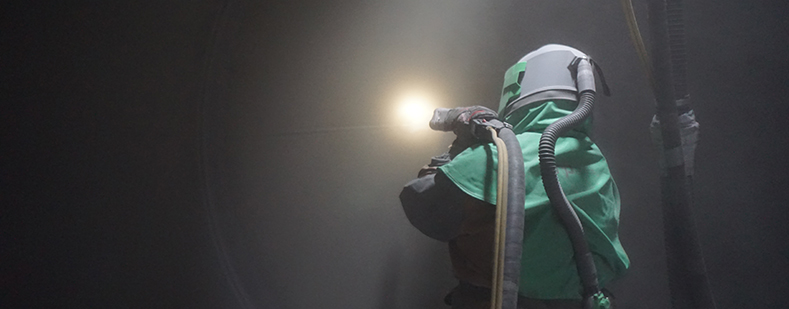
Contractors and facility managers alike agree that worker safety is the top priority when working on abrasive blasting job sites.From the depths of underground utility vaults to the interior of storage tanks, examples of confined spaces abound. Found in a wide range of industries and workplaces, each pose a unique risk to those who must enter them.
Read more >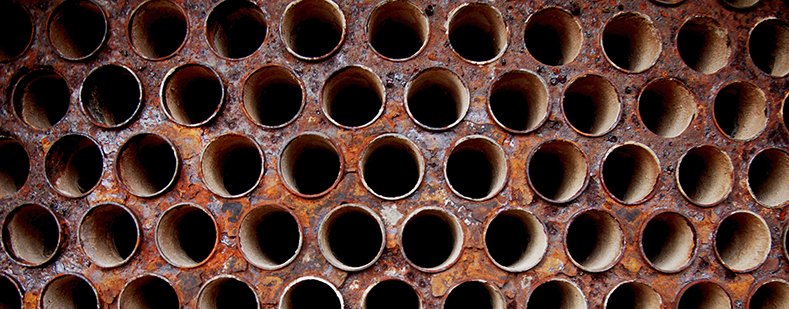
Facility maintenance professionals play a critical role in preventing corrosion within industrial settings, employing a range of proactive strategies to safeguard infrastructure and equipment. Upstream and downstream oil and gas, industrial manufacturing, wastewater treatment plants, among many other production facilities must all have a plan in place to delay the impact of corrosion's harmful effects.
Read more >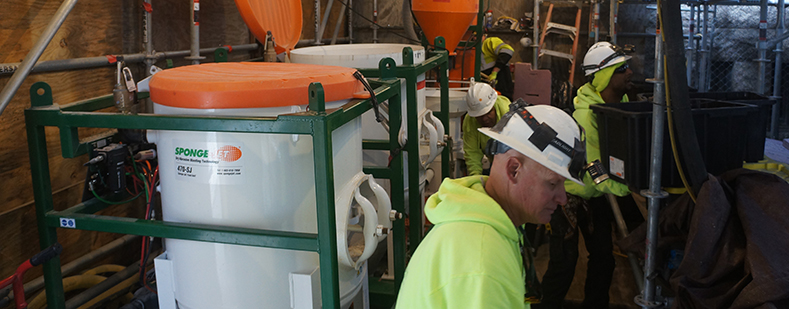
Choosing the best Sponge Media Feed Unit™ can seem like an intimidating task. Sizes, features, and portability vary between models, but they all do the same overall task of mixing blast media with compressed air for abrasive blasting. Some units like the EX product line are for use in potentially combustable, flammable atmospheres, while other units like the Rasp Xtreme and the 100-HP are optimized for portability.
Read more >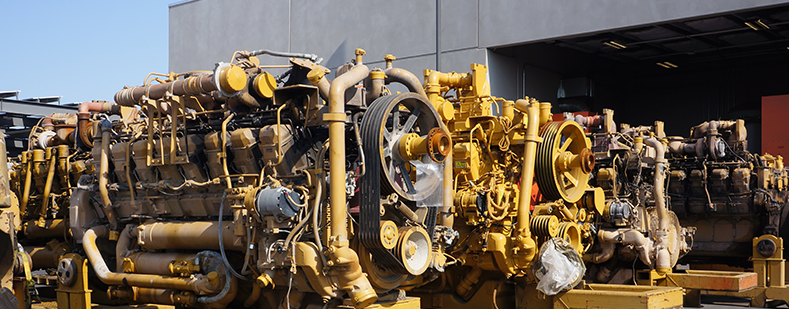
Many advanced Certified Rebuild Centers (CRCs) and Heavy Equipment Refurbishment facilities are turning away from regular abrasive blasting and/or high pressure washing during their re-manufacturing process. Increasingly, these centers are focusing on cleaning the equipment using Sponge-Jet blasting prior to disassembly.
Read more >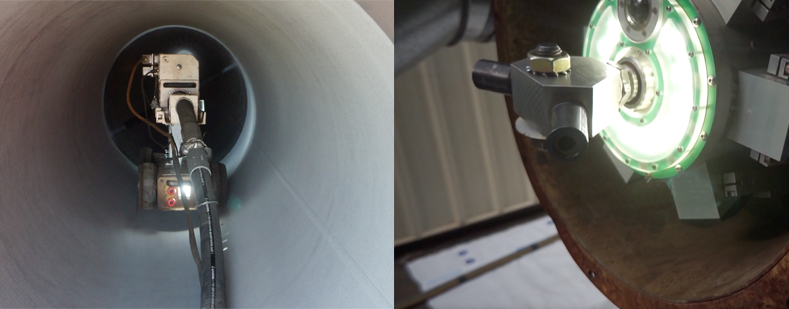
Now more than ever, Contractors are looking for ways to save money, increase worker safety, and reduce waste. For abrasive blasting projects like cleaning tanks, prepping pipe internals, or blasting walls and floors, robotic abrasive blasting is often a better choice than manual blasting.
Read more >