Building production capacity at Russia's largest steel and steel-related mining companies doesn’t happen without planning, staging, careful product selection and execution. PAO Severstal announced their plans to add a third blast furnace to the company’s Cherepovets Steel Mill in the Vologda Region, Russia. Corresponding with the install was construction of a wet cleaning scrubber and demister.
Read more >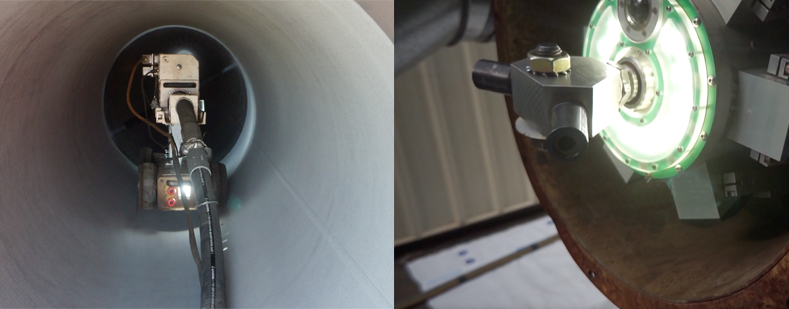
Now more than ever, Contractors are looking for ways to save money, increase worker safety, and reduce waste. For abrasive blasting projects like cleaning tanks, prepping pipe internals, or blasting walls and floors, robotic abrasive blasting is often a better choice than manual blasting.
Read more >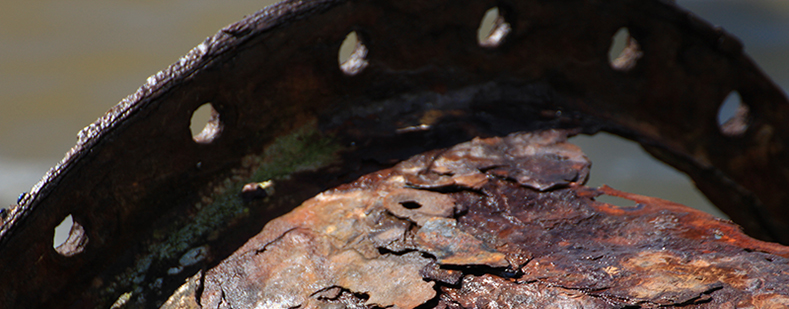
When paint starts to peel and bubble, it’s extremely important for the integrity of the asset to remove the old coating and apply a new one. As protective coatings fail, substrate corrosion can accelerate, leading to long term asset damage. If failed coatings and corrosion are not addressed, the damage may not be repairable and the asset may need to be replaced, ultimately costing the owner substantially more money.
Read more >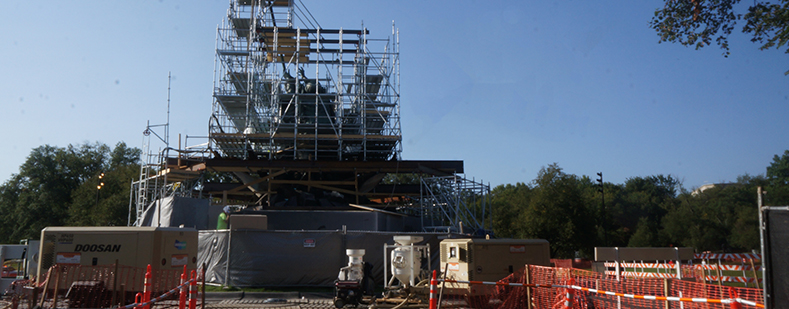
Abrasive blasters who have properly sized air compressors have the best chance for maximizing productivity and efficiency. Contractors and others who blast with mismatched air volume can suffer lost productivity and profits.
Read more >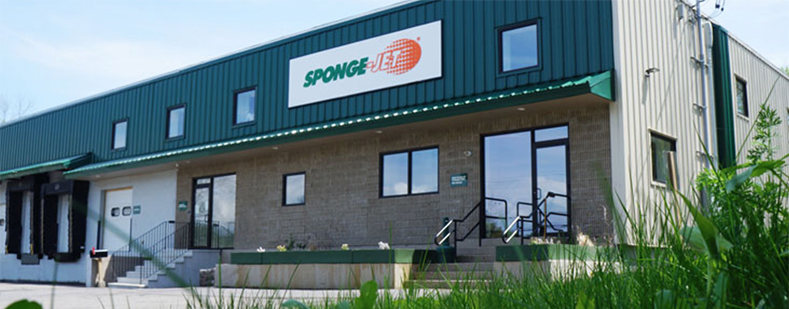
In this challenging and unprecedented time, Sponge-Jet is taking measures to ensure the health and safety of our employees as well as the continuation of business. Due to Sponge-Jet’s support of essential industry, especially corrosion prevention in defense, shipbuilding, power generation, oil and gas production, and the critical maintenance of buildings and infrastructure, we remain operational.
Read more >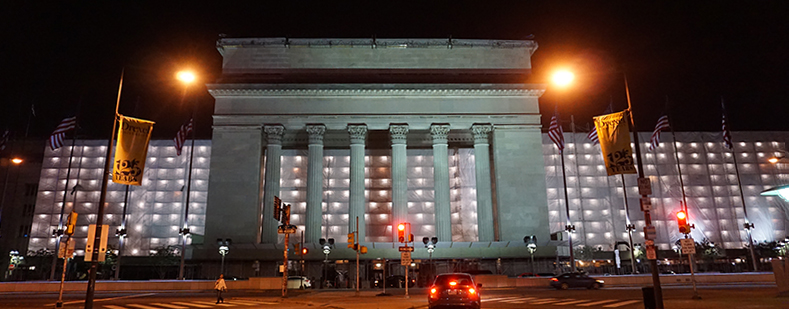
Lead paint removal is a challenge regardless of location and circumstances, but even more so when the process takes place in a busy train station. This was the case when Avalotis Corporation was tasked with a lead paint removal, surface preparation, and high-performance coating system application at the 30th Street train station in Philadelphia, PA.
Read more >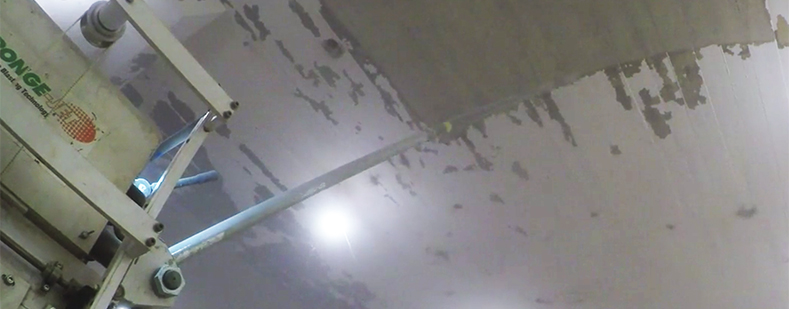
Robotic abrasive blasting is a great choice for projects in a wide variety of industries, including oil and gas, water and wastewater, the marine industry, and power generation plants. However, it is important to keep in mind that it is not just the industry itself, but also the application that determines whether robotic abrasive blasting is the right fit for a particular job.
Read more >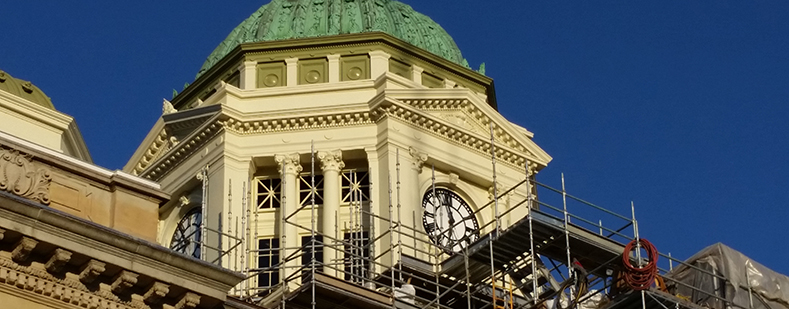
The Wyandot County Courthouse (Located in Upper Sandusky, Ohio, USA) is considered one of the best preserved examples of classical, turn-of-the-century architecture. Built in 1899, the courthouse was added to the National Historic Places in 1973.
Read more >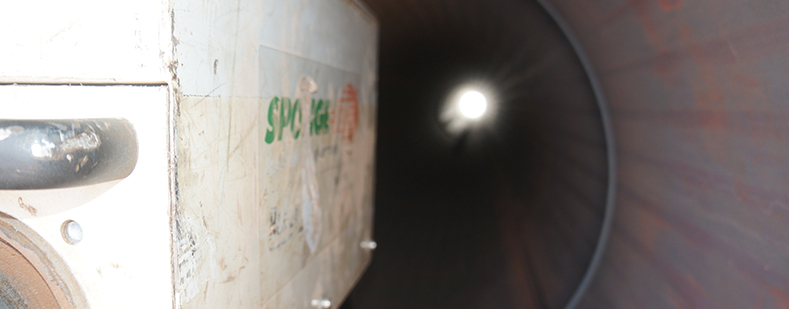
Worker safety is the number one priority on all abrasive blasting jobsites. Robotic abrasive blasting is one of the best ways to keep blasters safe while achieving optimal productivity and quality. Overall, robotic abrasive blasting with Sponge Media is a safer alternative to manual blasting in many situations.
Read more >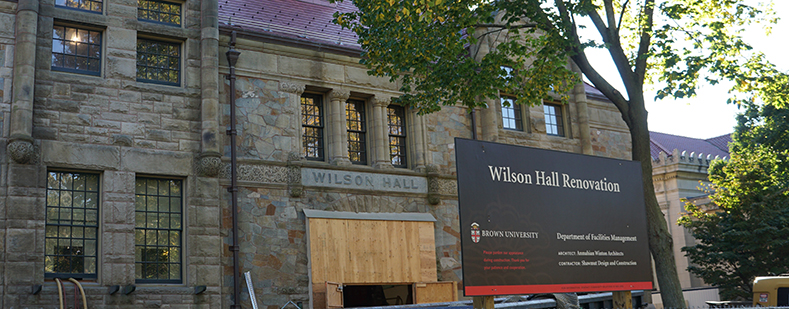
Wilson Hall (recently renamed Friedman Hall) is one of the most heavily used buildings on the Brown University campus. The Romanesque-style (circa 1891) structure was built at the bequest of George Francis Wilson and was designed by architects Gould and Angell to expand Brown’s lecture and classroom space.
Read more >