Many in the abrasive blasting industry rely on unaided visual assessments for their information. Tasks like identifying the level of cleanliness of a surface as Sa2.5 (NACE 2 or SP-10) during an inspection are required to be done with the naked eye by the included language, “when viewed without magnification". This is sometimes referred to as an “unaided view.” Often, an unaided view can be deceiving.
Read more >Sponge-Jet
Recent Posts
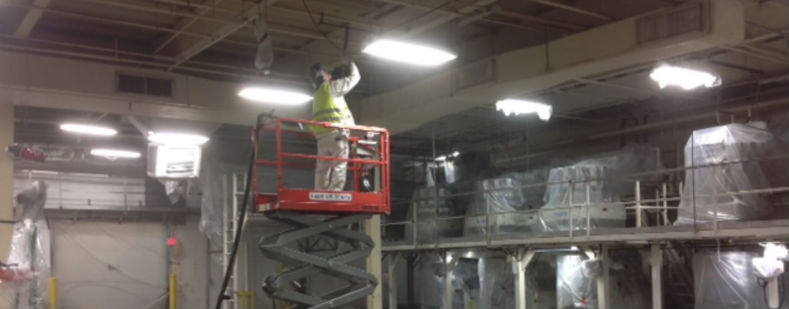
Many food processing plants have used Sponge-Jet to avoid contaminating equipment while cleaning their facilities. At a food processing plant in Georgia, many different kinds of substrates were cleaned, from concrete and steel to conduit and galvanized pipe. Layers of rust, salts, grease, and flaking paint were removed without water or chemical cleaning - a requirement of the facility owner.
Read more >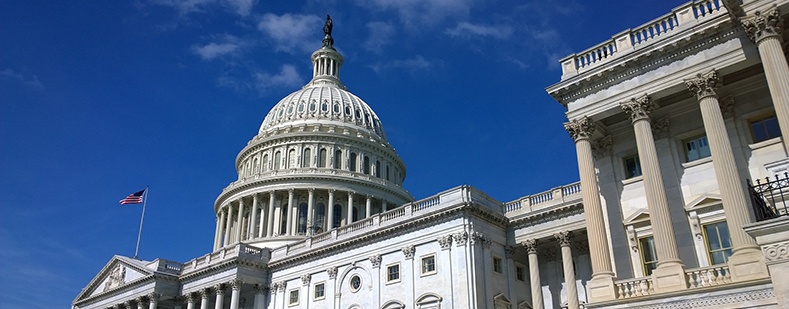
The work contractors and facility owners do using Sponge-Jet is often rewarding. Being a part of so many different applications and industries, from the building of battleships to returning fine art back into its gilded glory, our work is often hard to top. Perhaps this has been achieved on a project as important as the restoration of the U.S. Capitol.
Read more >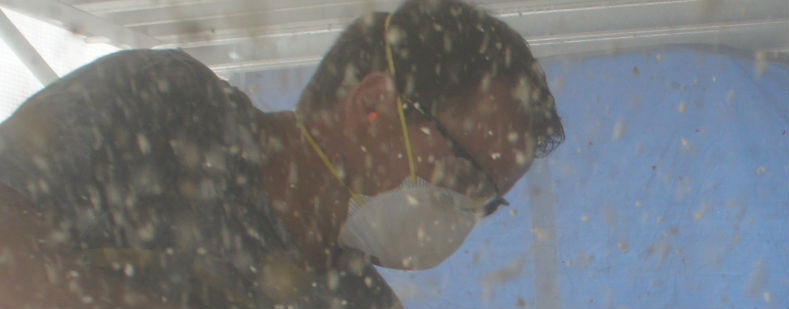
For over 80 years, industrial professionals have known of the health hazards that are created by sandblasting with silica sand, a once common sandblasting media. When blasting with sand, the particles fragment when they collide with the surface. This dust that is created frequently enters the lungs of the workers doing the blasting and those around them. Once in the lungs, this dust creates a number of ailments, most notably silicosis which can lead to death. Due to these issues, many European countries have banned silica sandblasting - some as early as 1947.
Read more >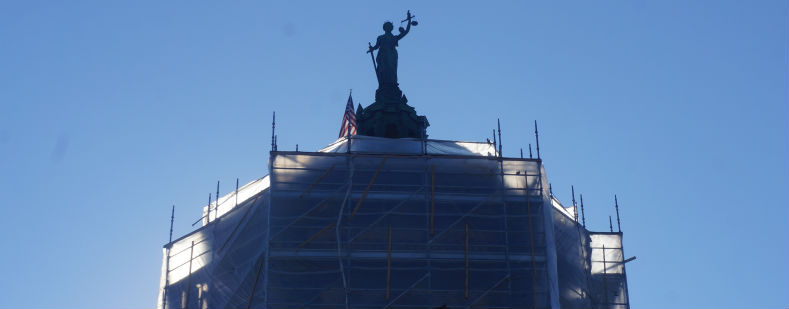
From Duluth, Minnesota to Washington DC through Europe and South-East Asia, Sponge-Jet has seen a large number of cities and states use micro-abrasion technology to preserve and restore historic buildings and structures.
Read more >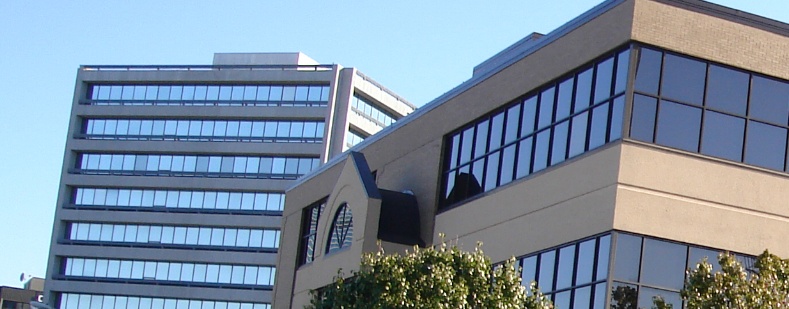
Contractors charged with restoring large buildings often have the time consuming task of repairing and/or repainting window frames and casings. Windows in these buildings can be very heavy and fragile, with glass components highly susceptible to chipping or fracturing. Window damage is avoided at all costs, as the glass is very costly to replace and reinstall.
Read more >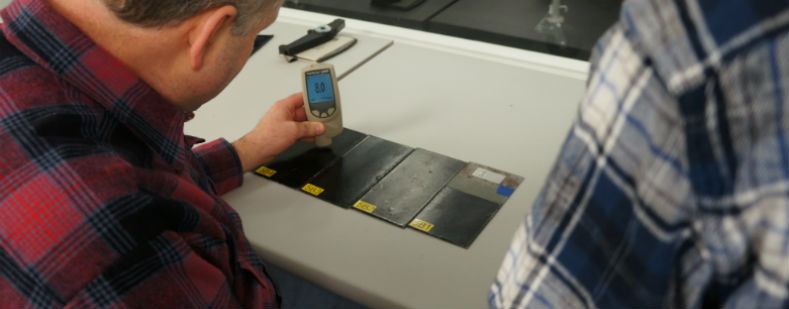
If there was a college major for the coating of metal substrates, the first class would be Surface Preparation 101. The main theme would be maximizing coating adhesion…and to do this, a number of criteria would be taught including visual cleanliness, removing invisible contamination (salts/chlorides, oils, grit embedment), and how to create the coating’s required surface profile.
Read more >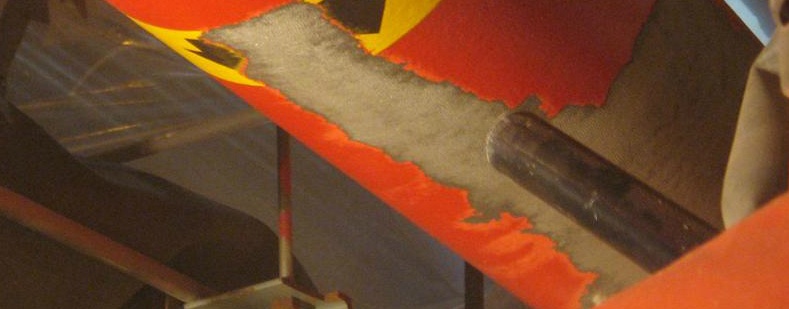
It’s a common belief in the industrial and manufacturing industries that all sparks create a hazard. Sparks can represent poor equipment grounding, short circuiting, or friction and collision energy that can be harmful to workers and machinery. Many also believe that all sparks can create an explosion through combustion in an explosive or flammable environment. While sparks can ignite flammable solids, liquids, or gasses, not all sparks possess the energy to cause an explosion.
Read more >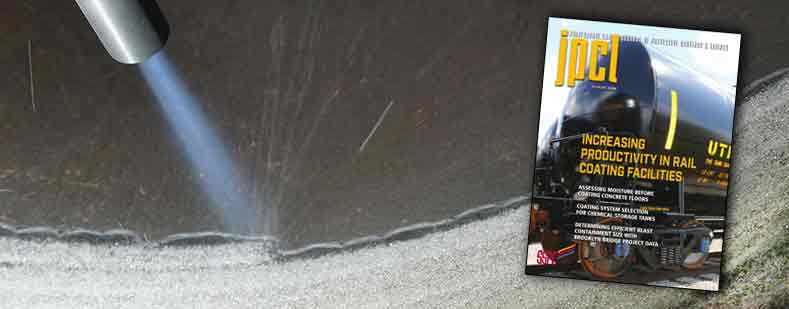
Jim Molnar, Chairman of the Mechanical Association of Railcar Tank Services (MARTS) and industry-expert, Ed Zaharias quickly preview Sponge-Jet Robotic tank car cleaning technology along with other industry updates in the latest issue of JPCL. The article notes “encapsulated media blasting” aka Sponge Blasting technology as a way to increase productivity in rail coatings and lining facilities. Both Sponge Media™ abrasives and the Robotica™ tankcar robot are highlighted.
Read more >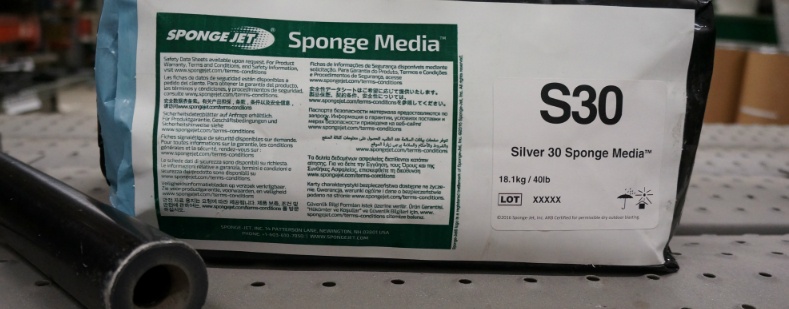
The new labeling system translates important product information in 15 languages, providing access/locations to Safety Data Sheets (SDS), safety information, and terms and conditions.
Read more >