Facility maintenance professionals play a critical role in preventing corrosion within industrial settings, employing a range of proactive strategies to safeguard infrastructure and equipment. Upstream and downstream oil and gas, industrial manufacturing, wastewater treatment plants, among many other production facilities must all have a plan in place to delay the impact of corrosion's harmful effects.
As long as humankind has used tools made from metals such as bronze and iron, they've fought corrosion. While ancient people used wax and fat to protect their tools, modern corrosion defenses are a bit more advanced. Billions of dollars have been invested into the development and application of coatings systems.
As taught by AMPP, the Association for Materials Protection and Performance, no liquid applied coating is impermeable. This means corrosion can happen under coatings - even very technically advanced, expensive coatings. Blisters, peeling, and pinholes in paint are usually the result of impropper surface prep. Occasionally these issues are the result of poor coatings application, but according to AMPP, improper surface preparation can be blamed for 70% of all coatings failures.
Those that do not invest in surface preparation face a much higher chance of corrosion, causing significant harm to structures and equipment. The result: much higher maintenance and repair costs. When the cost of corrosion is taken into account, use of Sponge Media for surface prep may be the most important thing you can do for your bottom line.
According to the AMPP, the direct cost of corrosion in the United States alone is estimated to be between $276 billion and $558 billion annually.
This cost includes expenses related to maintenance, repairs, replacements, and lost productivity. For example, if a piece of equipment fails due to corrosion, it may need to be replaced, leading to additional costs and downtime. Similarly, if a pipeline corrodes and leaks, it can cause environmental damage and result in costly cleanup efforts.
What does improper surface prep look like? Here are a few of the common mistakes that lead to a 2.5 trillion dollar problem globally:
-
Incomplete removal of contaminants: If contaminants such as oils, grease, salts, or rust are not fully removed during surface preparation, they can act as a catalyst for corrosion, leading to rust formation and metal degradation.
-
Poor surface profile: If the surface profile is not within the recommended range, coatings and other materials may not adhere properly, leaving bare metal exposed to the elements, which will soon result in surface corrosion. Over time, this will devolve into a much bigger issue impacting overall integrity.
-
Improper priming: If the surface is not primed properly after blasting, coatings and other materials may not adhere properly, leaving bare metal exposed to the elements, which can lead to corrosion.
Sponge Blasting is the only method of surface prep that simultaneously removes contaminants, corrosion, old coatings, and profiles the surface for recoating.
Specifiers and Corrosion Engineers around the world agree, Sponge Media's ability to remove visible and invisible contaminants such as rust, grime, oils, and chlorides is unmatched. These "Sponge Prepped" substrates are an investment in the fight against corrosion and coatings failure.
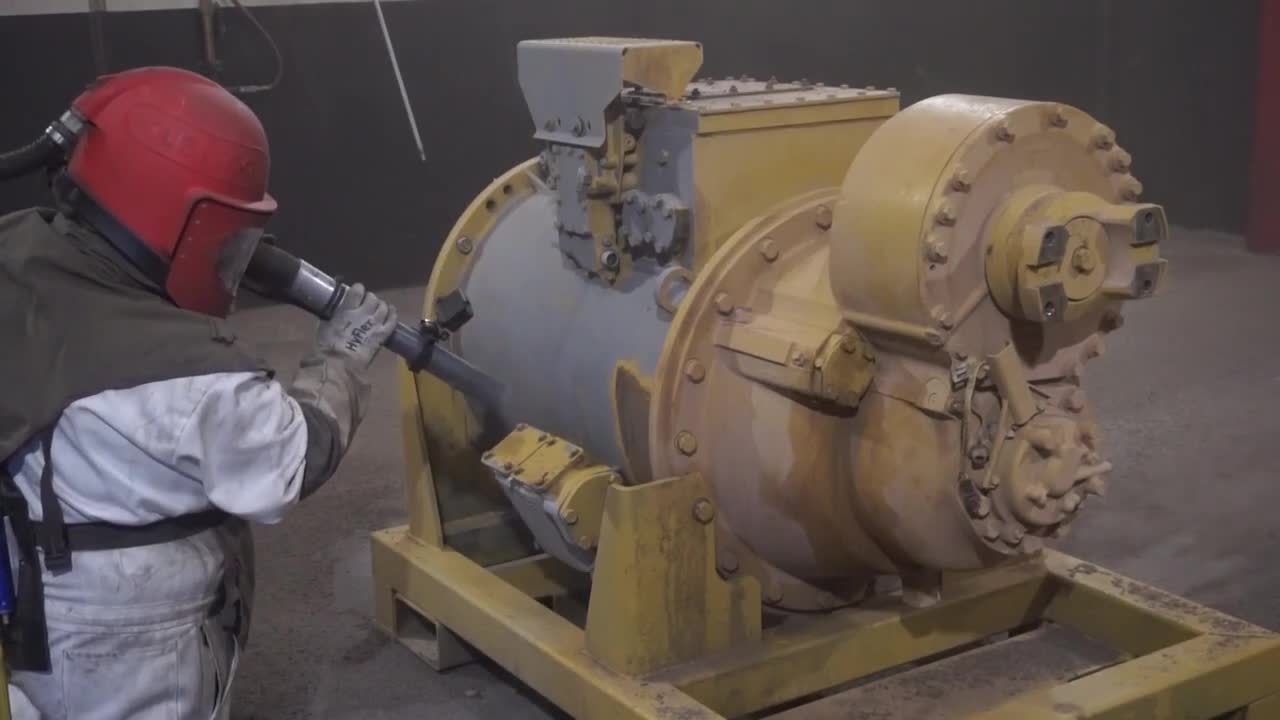